The blue-and-yellow tugs of Western Towboat are fixtures in the Seattle area. But harbor work on the West Coast is only a fraction of the company’s business. Its biggest job is freighting more than a billion pounds of goods each year to Alaska.
The lifeline for Southeast Alaska begins in the Lower 48. Most of the coastal communities along the Last Frontier’s panhandle have exactly zero roads connecting them to the outside world. Which means that nearly everything (except fresh fish, native salmonberries, and a few other goods) must come by water, most of it packed in containers at a Seattle dock, stacked six-high on a barge, and towed north through the Inland Passage.
“That’s how we get our beer—once a week, all year long, on a barge,” says Jackie, who’s been tending bar at the Fogcutter Bar in Haines, Alaska for the past 13 years. “We’re always happy to see that barge come in.”
Nearly everyone relies on the barge service in some form. Peace Health Medical Center in Ketchikan needs certain vaccines that are restricted from airfreight, so they’re barged in. The Alaskan and Proud grocery store chain relies on the barge service for fresh produce. Cars, building materials, heavy equipment—as much as 1.5 billion pounds of goods each year are floated in on shipping highways connecting Alaska with everyone else.
The primary transporter of goods is Alaska Marine Lines, part of the Lynden family of companies that handles the bulk of air, land, and sea freighting to Alaska, Russia, and Western Canada. Lynden’s barge service to Southeast Alaska has essentially supported the growth and development of the area. And making that happen since the early 1960s, delivering the cargo every week from Seattle to the small towns and settlements from Ketchikan to Whittier have been the steady, impeccable workhorses of Western Towboat, a fleet of tug boats custom-built for long-haul towing through some of the toughest Pacific shipping routes.

“We’re the mailmen for Southeast Alaska,” says Russell Shrewsbury. Russell and his brother, Ross, who are both third-generation tugboat captains, joined their father, Bob, as part owners of Western, along with their sister, Kristin, about five years ago. “As the area has grown, so have we. As Southeast Alaska has expanded and gotten bigger, so has our business in order to fill their needs.”
On Wednesdays and Fridays, Western tugs pull out of Seattle bound for Alaska with as much as 30 million pounds of containerized cargo on a barge. Many of the containers will be refrigerated. Mining equipment is sometimes part of the load. Manufactured houses and school buses can be placed on top of the stacked containers. The whole affair will be lashed to the barge deck with chains and turnbuckles for the journey north.
The tugs begin the run to Southeast Alaska (Western’s barge service to Whittier is a different route) with a three-day passage off the coast of British Columbia, skirting the open Pacific and steaming hard for the first port of call, Ketchikan. When running through open water the tugs play out the tow cable to as much as 1,000 feet. A three-inch-chain bridle (meaning the link steel is thee inches in diameter and each link is about a foot long) on the front of the barge helps manage the slack and tension between the tug and the barge.

As it nears port, the tug reels in the two-and-a-half-inch tow cable, slows the load, and prepares to guide the barge into port without assistance, something most tugs can’t do. With the barge slowed to only a few knots, the tug swings alongside and makes up, or ties itself, to the side of the barge. The maneuver is called flopping alongside, and the tug’s new position on the barge is called riding on the hip. While made fast to the hip, the tug guides the barge into the dock.
The only reason these tugboats can handle the barges alone is because of their two propellers, called z-drives, that can be rotated 360 degrees to provide thrust in any direction. The boats have no rudders or keels. The propellers are eight and a half feet in diameter and enclosed in a pipe-like shroud. The tugs are among the strongest and most maneuverable in the industry.
“They’re hands down the best boats in the business for what they do,” says Captain Neil McGourty, who’s been at Western for the past 13 years and been skippering tugs to Alaska for the past five. “The Ocean Titan is a 5,500 horsepower, z-drive ocean-going tug. It’s 120 feet long, and you can spin it around in a matter of seconds. It’s a badass rig, for sure.”

Western Towboat, founded in 1948, built its first tug, the Western Mariner, in 1982. It now has 22 boats in its fleet, seven of which are Titan-class tugs, Western’s unique class of tugboat first built in 1997 by owner Bob Shrewsbury, Ed McEvoy and the naval architects at Jensen Maritime. Many others have since copied the design, and the crew at Western aren’t the only ones who think they’re the best as what they do.
“The Titan class ocean-going tugboats developed by Western Towboat, in concert with Jensen Maritime, are the premiere barge-towing tugs on the West Coast,” says Robert Dorn, CEO of the marine transport company Hyak Maritime. “Hyak has three [Titan-class tugs], Harley Marine has three, the Kirby Corporation has two, and more will be built in coming years.”
With every boat it builds, Western’s Titan-class tugs get better. Each boat is the result of an effective collaboration of minds—captains, engineers, deckhands, mechanics, naval architects—on how to make the boat a better tool for the job. The improvements are too many to list: articulating wheelhouse towers that negate time waiting for a draw bridge; the extensive use of stainless steel to reduce the time and cost of repairs and maintenance due to rust; winch systems operated by the pilot in the wheelhouse so no one has to man them on deck.
The Titan-class tugs are at their finest when towing or landing barges in the narrow, weather-beaten ports of Southeast Alaska. Each freight run lasts ten or 11 days, with nine or ten ports of call along the way. At Ketchikan, the first stop, the barge will take on a forklift and container lift for loading and unloading the freight along the way. The barge will be in port for four or five hours, handling the containers in an all-hands-on-deck operation, though one of the crew is usually sleeping to be ready for a later watch. With a lighter load, the tug steams out of Ketchikan and on toward the next port, through the narrow channels of the Coastal Ranges, where the mountains pitch into the sea at near-vertical angles and the fog slides in on a carpet of wind.

Sometimes the weather is good, and sometimes the seas are calm. But no one counts on that for very long in Southeast Alaska.
“The weather is the hardest thing we deal with,” says Captain Neil McGourty. “If it were flat calm all the time, the job would be relatively easy.”
From Ketchikan, the tugs work their way toward Skagway, the port farthest north on the run. The boats consume about 48,000 gallons of diesel fuel on the run. The crew burns through about ten pounds of coffee. The cribbage board is always on the mess table, and the loser’s debts are always tallied on a whiteboard in the galley, guaranteed to be paid.
The tugs navigate through the Frederick Sound, the Wrangell Narrows, and the Lynn Canal; passed breaching humpback whales, coursing dolphins, and the LaConte Glacier; from Ketchikan to Petersburg to Juneau to the Kensington Mine to Haines, and then to Skagway, where the tugs turn south for their return.
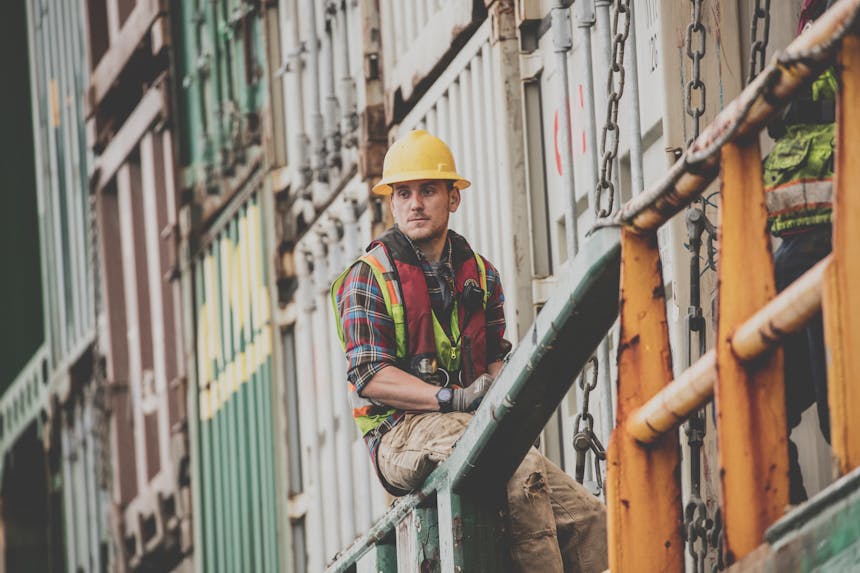
About 30 captains drive tugs for Western Towboat, some of them driving the route to Whittier, Alaska, some of them handling harbor work all along the West Coast, and some of them making the Ketchikan-Skagway run. Freight service to Alaska is about 70 percent of the company’s business, and continues to be a vital supply chain for the communities it serves. The boats don’t come home empty, though.
In Juneau, for instance, the barges take on refrigerated containers of fresh fish, headed for both foreign and domestic markets. Once in Seattle, many of the containers will be loaded on huge ships bound for Asia. But some of the containers will stay in the U.S., and not all of them are full of fish.
“If you’ve ever had an Alaskan Amber beer, they ship with the Lynden Company, which we tow barges for,” says Russell Shrewsbury. “So the Lower 48 gets to enjoy that beer because of us.”